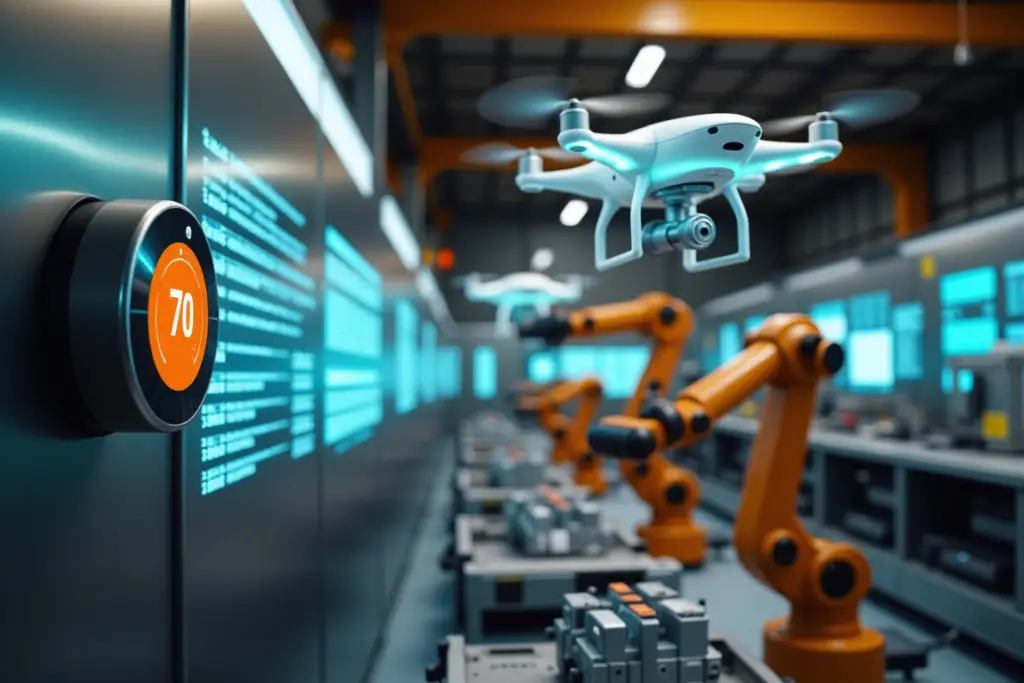
Control systems are the backbone of many technologies we rely on every day. From controlling the temperature in your home 🌡️ to the movement of robots in manufacturing plants 🤖, control systems ensure precision and stability in a wide range of applications. Let’s explore the different types of control systems and how they work in real-life scenarios.
1. Introduction to Different Control System Types
Control systems can be categorized into two main types: open-loop and closed-loop systems. Each type has unique characteristics that make them suitable for different tasks.
Open-Loop Control Systems
Open-loop control systems operate without feedback. The system doesn’t check if its actions achieve the desired result. Instead, it simply executes commands based on a fixed input.
Example: A toaster 🍞 is an open-loop system. It works by simply heating the bread for a set amount of time, regardless of how toasted it actually is.
Closed-Loop Control Systems
Closed-loop systems, on the other hand, use feedback to adjust their operation and ensure the desired output is achieved. These systems measure the output and make adjustments as needed.
Example: Thermostats 🏠 are closed-loop systems. They monitor room temperature and adjust the heating or cooling system to maintain the set temperature.
2. Feedback Control
Feedback is essential in closed-loop control systems. It allows the system to make real-time adjustments to stay on track. Feedback can be either positive or negative:
- Positive Feedback: This type of feedback amplifies changes. It’s used in systems that need to accelerate a process, such as in microphones 🎤 or amplifiers.
- Negative Feedback: Reduces or counteracts changes, helping maintain stability. This is common in temperature control systems 🌡️.
3. PID Controllers
PID controllers are among the most widely used control systems in modern engineering. PID stands for Proportional, Integral, Derivative, and these three components work together to adjust a system’s output.
PID Component | Purpose | Example |
---|---|---|
Proportional (P) | Adjusts output based on the error (difference between desired and actual output) | Balancing a robot 🤖 |
Integral (I) | Corrects past errors that are accumulating over time | Temperature regulation 🌡️ |
Derivative (D) | Predicts future errors to prevent overshooting or undershooting | Speed control in cars 🚗 |
Example: In robotics 🤖, PID controllers help robotic arms move smoothly by adjusting their motion to ensure precision.
4. Fuzzy Logic Control Systems
Fuzzy logic systems mimic human reasoning, where decisions are not based on rigid criteria but on approximate reasoning. These systems can work with imprecise data and make decisions based on a range of values.
Example: Washing machines 🧺 with fuzzy logic adjust wash cycles based on load size, fabric type, and dirt level, without needing precise values. Instead, they make a “fuzzy” decision based on available information.
5. Adaptive Control Systems
Adaptive control systems can change their behavior over time in response to environmental changes or system performance. Unlike traditional control systems that remain static, adaptive systems “learn” from their environment and make real-time adjustments.
Example: Drones 🛸 use adaptive control to compensate for wind changes, making adjustments to stay on course even when the environment fluctuates.
6. Examples of Real-World Applications
Control systems are used in many areas, improving efficiency and ensuring that processes run smoothly. Here are a few examples of how control systems work in the real world:
Temperature Control Systems
Closed-loop systems like smart thermostats 🏡 automatically adjust home temperatures, ensuring comfort without wasting energy.
Automated Manufacturing
In factories, robots 🦾 are controlled by systems that ensure precision and efficiency, from assembling products to welding parts. Closed-loop systems adjust robot movements based on feedback from sensors to ensure they perform tasks accurately.
Aerospace
In aviation ✈️, autopilot systems automatically control the flight path of aircraft, adjusting speed, altitude, and direction based on real-time feedback.
Smart Appliances
From refrigerators 🧊 to air conditioners ❄️, smart appliances use control systems to adjust their operation based on sensors, ensuring energy efficiency and comfort.
7. Challenges of Control Systems
Although control systems bring many benefits, they also present certain challenges:
Challenge | Impact |
---|---|
Complexity | Designing adaptive or fuzzy logic systems can be complex. |
Cost | High-quality components like sensors and controllers can be expensive. |
Maintenance | Regular calibration and maintenance are required to keep systems running efficiently. |
Cybersecurity | Internet-connected control systems face security risks from cyberattacks. |
8. Future Trends in Control Systems
The future of control systems is exciting, with several trends shaping their evolution:
- Artificial Intelligence (AI) 🤖: AI-powered systems will enable control systems to learn from past data and improve their performance autonomously.
- Internet of Things (IoT) 🌐: IoT devices, like smart sensors, will integrate with control systems to create seamless, real-time decision-making across industries.
- Self-Healing Systems 🔧: Future systems will be able to detect faults and make repairs automatically, improving reliability and reducing maintenance costs.
Conclusion
Control systems are at the heart of modern automation, ensuring stability and efficiency across various industries. Whether it’s a robot assembling products or a thermostat adjusting your home’s temperature, these systems allow us to automate complex tasks and make informed decisions. As technology advances, control systems will become even smarter, more adaptive, and more integrated into our daily lives. The future promises exciting possibilities, from AI-powered systems to IoT-driven automation.